Mehr Produktionskapazität mit dem Pegasus-Mischer
Dinnissen baut neue Mischanlage für Solan Kraftfutterwerk
Mehr Produktionskapazität mit dem Pegasus-Mischer
Dinnissen baut neue Mischanlage für Solan Kraftfutterwerk
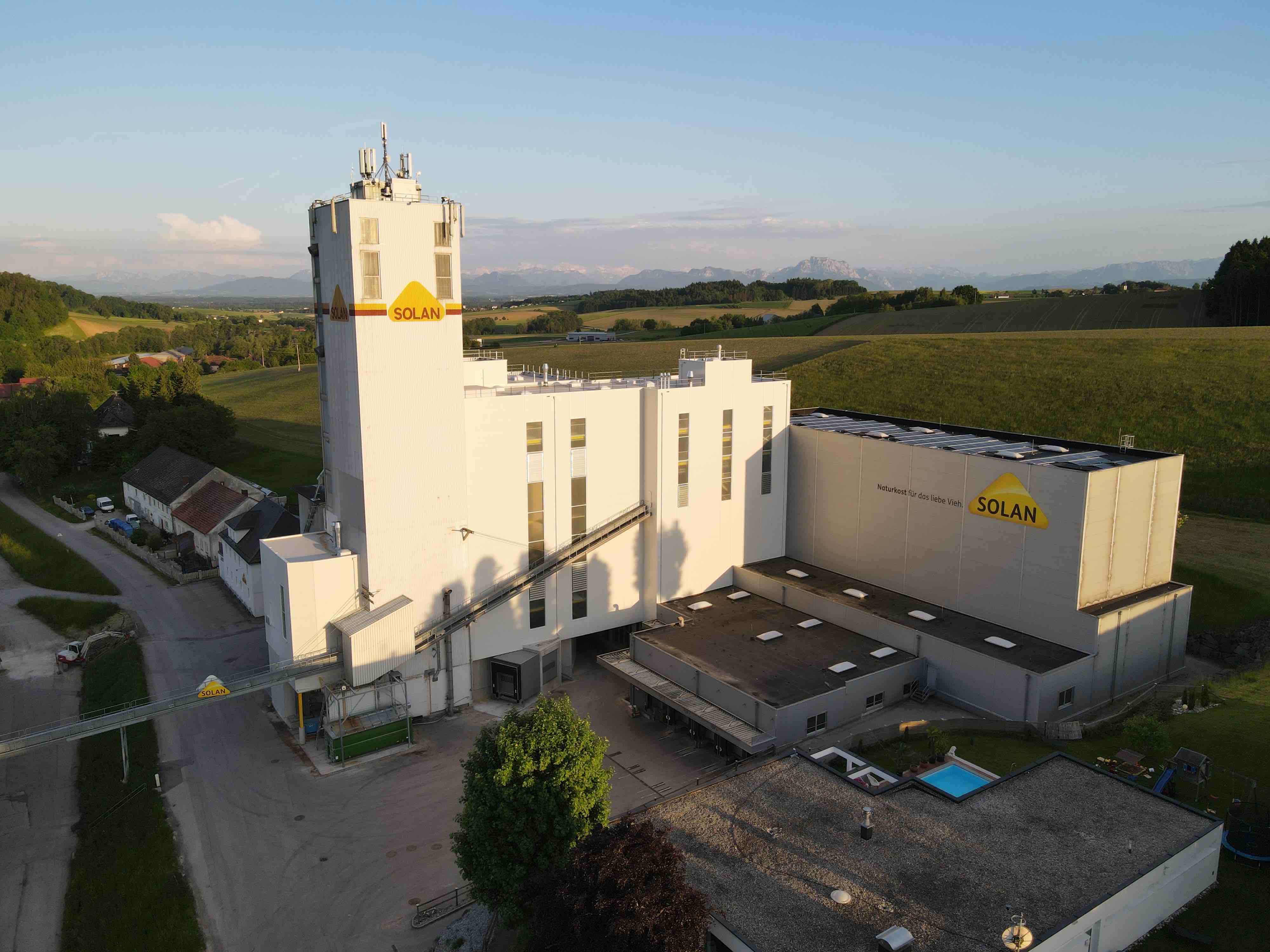
Mehr Produktionskapazität mit dem Pegasus-Mischer
Dinnissen baut neue Mischanlage für Solan Kraftfutterwerk
Das Solan Kraftfutterwerk ist einer der führenden Tierfutterhersteller Österreichs. In Zusammenarbeit mit Dinnissen hat Solan eine Produktionslinie für Mineralfutter entwickelt und damit gute Erfahrungen gemacht.
Harald Schmalwieser, Geschäftsführer des Solan-Kraftfutterwerks in Bachmanning, Österreich ist von der Zusammenarbeit mit Dinnissen Process Technology überzeugt: "Wir haben unsere Produktionskapazität vervierfacht, von drei auf 12 Tonnen pro Stunde.“ Die effektive und präzise Flüssigkeitsdosierung war für den Unternehmer ausschlaggebend dafür, einen Mischer von Dinnissen einzusetzen. Dank der neuen Mischanlage sank die Transportzeit pro Charge von 20 auf 2,5 Minuten.
Gemeinsam mit seinem Engineering Planer Günther Tschurnig entwickelte er einen "Masterplan" für eine Modernisierung des Werkes. In diesem Zusammenhang wollte Harald Schmalwieser unter anderem die Mineralfutter- und Premixanlage verbessern. Dabei sollten vor allem während des Mischvorgangs Flüssigkeiten hinzuzufügen sein. In der alten Anlage musste dafür ein separates System für die Homogenisierung des Produkts eingesetzt werden. Das war zeitaufwendig und ineffizient. Außerdem sollte die neue Anlage die Möglichkeit zur schnellen und vollständigen Entleerung bieten, kombiniert mit kurzen Mischzeiten und variablen Füllmengen.
Game changer
"Die Suche nach einem Fertigungspartner, der unsere Anforderungen erfüllen konnte, war ein schwieriger Prozess. Wir haben drei Systeme von verschiedenen Unternehmen verglichen“, so der Firmenchef. Dinnissen hob sich von den anderen Unternehmen ab. Sie boten die beste Lösung an und gingen zudem aktiv auf die Bedürfnisse und Anforderungen von Solan ein. Erste Versuchsmischungen mit den verschiedenen Produkten im Technikum von Dinnissen verliefen positiv. Zudem hatte Dinnissen mit dem Pegasus-Mischer eine Lösung, die 600 bis 1.500 Kilogramm pro Charge mischt. Das komplexe System der direkten Flüssigkeitszugabe ermöglichte es, sieben verschiedene Flüssigkeiten vollautomatisch in den Mischprozess einzubringen. Dieses Flüssigkeitszugabesystem war für Solan ein „game changer". Solans Erwartungen an die neue Anlage wurden mehr als erfüllt.
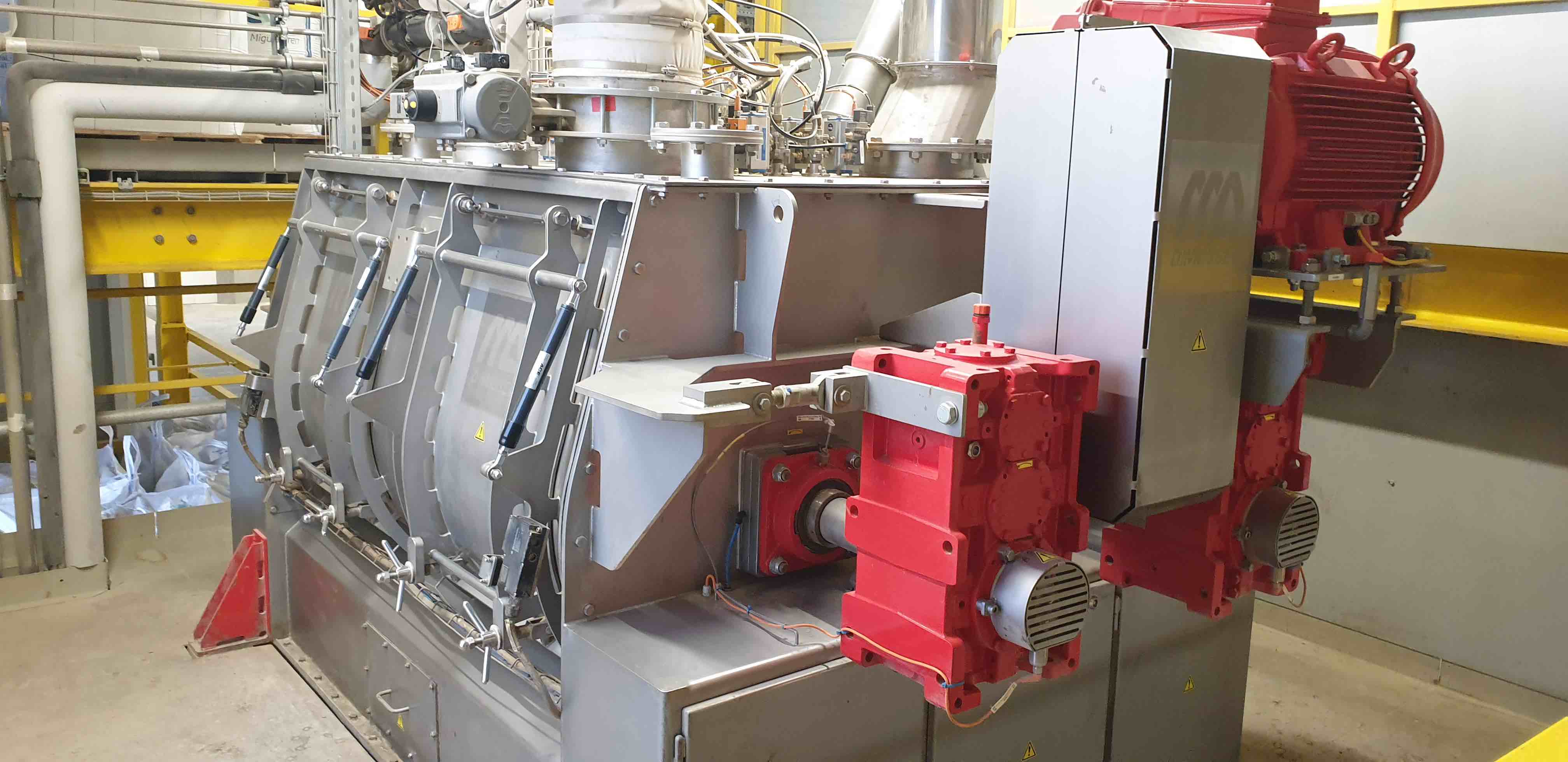
Schonend und sicher
Der Mischer arbeitet sehr schonend. Das ist im Prozess wichtig, damit die verschiedenen Zutaten während des Mischvorgangs intakt bleiben. Der Mischer ist mit vier Türen ausgestattet und kann so relativ gut gereinigt werden. Das hilft, Hygieneanforderungen zu erfüllen. Eine schnelle und einfache Reinigung ist sehr wichtig bei häufigen Produktwechseln. Da Solan verschiedene kleine Chargen mit unterschiedlichen Zutaten für verschiedene Kunden produziert, ist dies von großem Vorteil. Mit neuen Dosiersilos und einer zusätzlichen Chargenwaage, kombiniert mit sehr effektiven Aspirationsanlagen wird die Freisetzung von gesundheitsschädlichen Elementen verhindert und die Sicherheit für die Mitarbeiter verbessert.
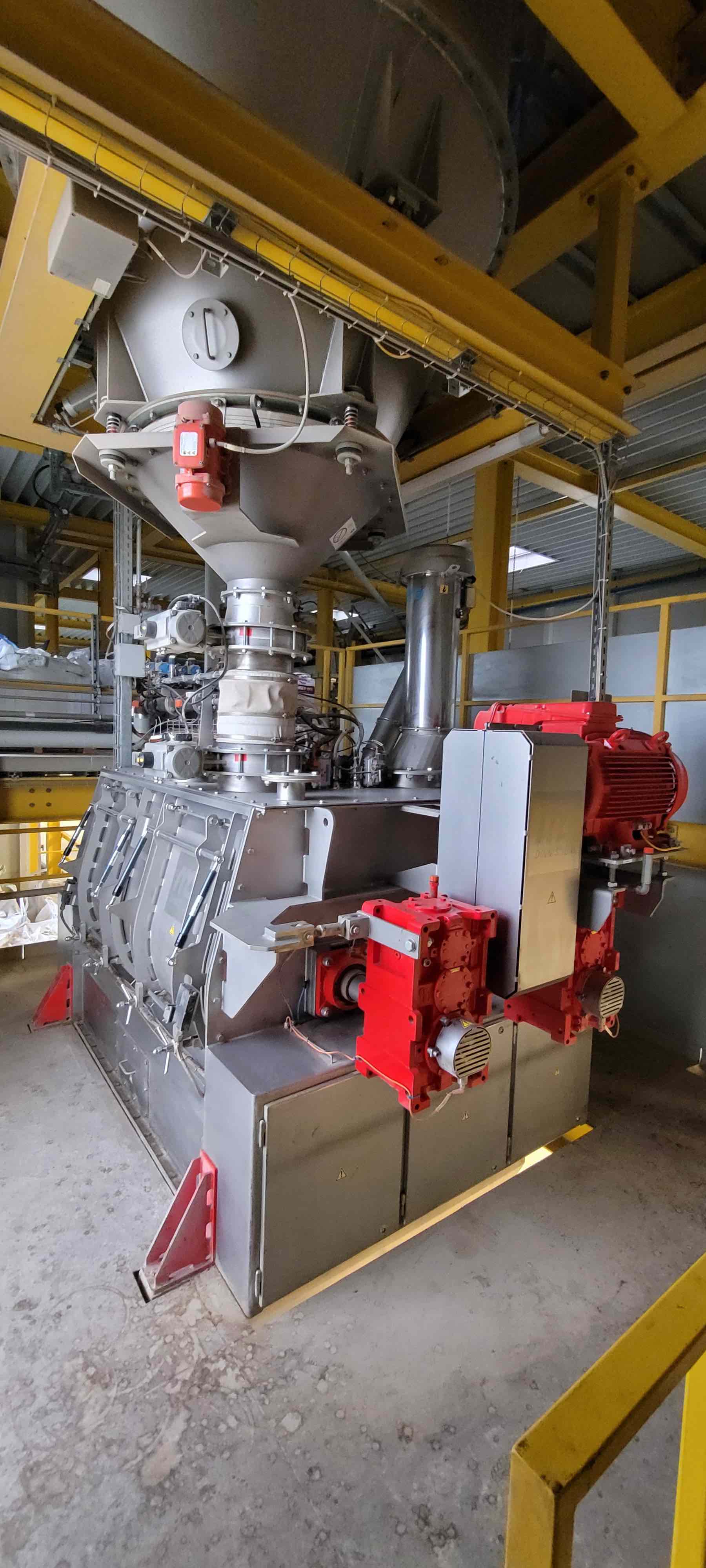
Problem Reinigungszeit
Beide Unternehmen arbeiten immer noch kontinuierlich zusammen, um die Systeme weiter zu optimieren. Wird in der Mischanlage Melasse in den Mischprozess eingebracht, führt dies zu hartnäckigen Verunreinigungen. Die einzige Möglichkeit, diese Verunreinigungen zu entfernen, ist die Trockeneisreinigung. Diese Reinigung ist zeitaufwendig, teuer und energieintensiv. Bei Solan wird jede Woche die Anlage gereinigt. Verständlich, dass man den Prozess verkürzen möchte.
Melassiertes Mineralfutter ist ein schwieriges Produkt, das in sich reagiert und schwer zu reinigen ist. „Es gibt selbstverständlich Lösungen, um die Reinigungszeit zu verkürzen“, erklärt der bei Dinnissen zuständige Projektmanager Piet van Bommel „doch die müssen sich für ein Mischfutterwerk im finanziellen Rahmen bewegen. Die Lösungen, die wir für den Lebensmittelbereich haben, wären zu teuer.“ Aktuell arbeitet man aber an einer Verbesserung für Solan, die sich aber noch bewähren muss.
Unternehmer Harald Schmalwieser bestätigt, dass die Anlage bisher im Alltag „sehr zufriedenstellend“ arbeitet. Wenn, dann sei nur das Thema Reinigung problematisch. Aber „wir arbeiten noch daran. Unter anderem an alternative Komponenten zu Melasse“, erläutert er das weitere Vorgehen dazu. Er würde sich jedenfalls immer wieder für Dinnissen Process Technology als Partner entscheiden.
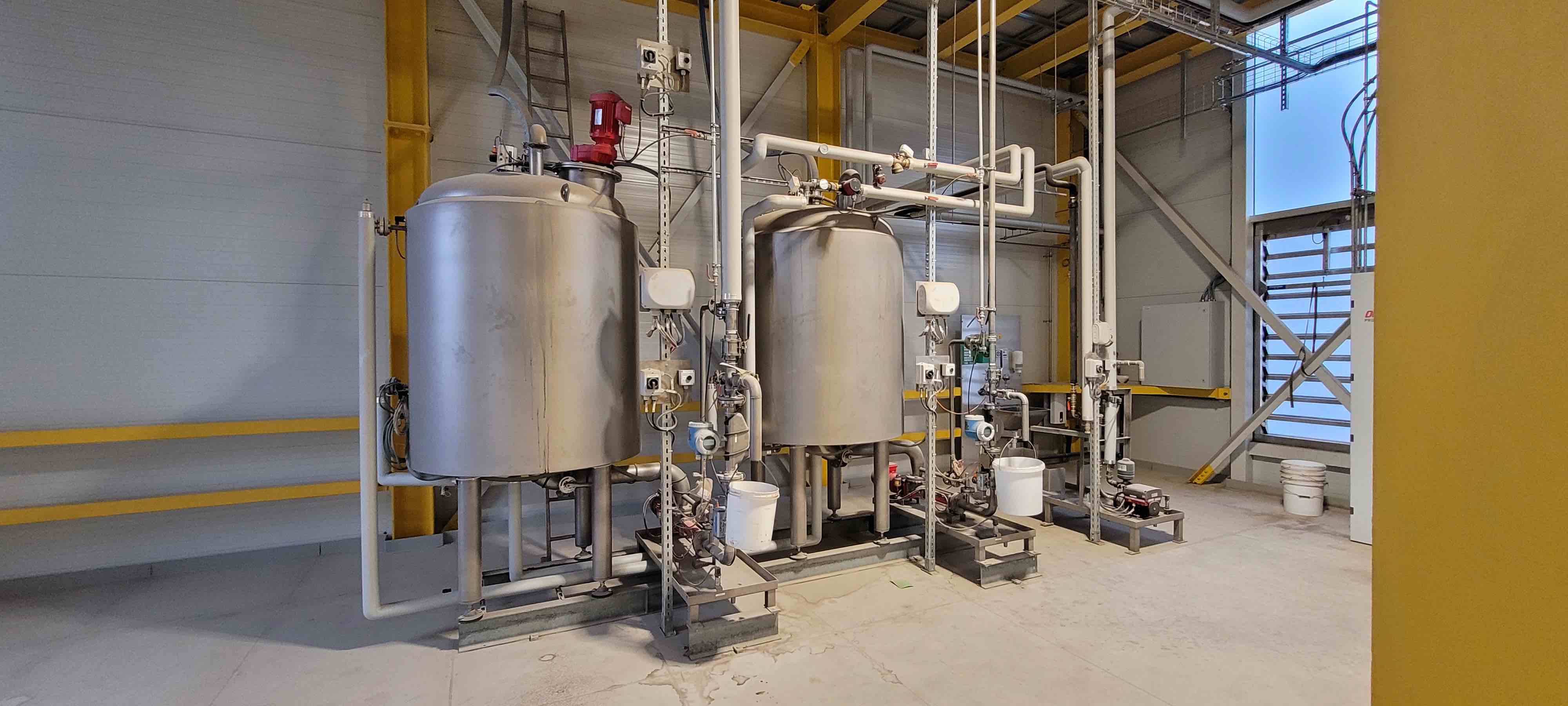
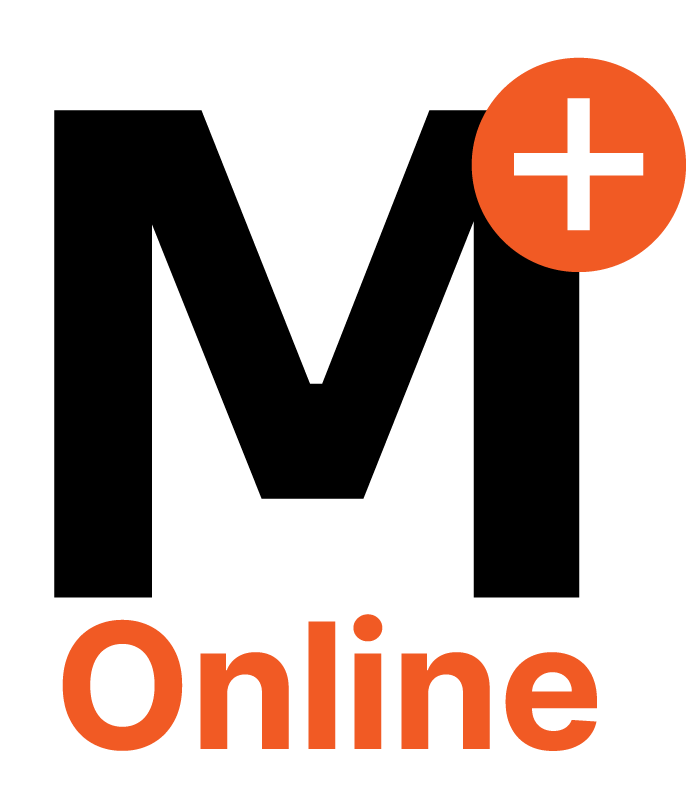